The Metal Processing Magazine and Harbin University of Science and Technology jointly compiled the "Guide to the Selection of CNC Tools", which carefully included the CNC tool product information provided by Sandvik Coromant, Zhuzhou Diamond, Iskar and other famous domestic and foreign tool manufacturers. Mold processing is one of the overall solutions for the application area. If you want to fully understand the specific content of this book, please go to the metal processing professional online shop (Taobao search "CNC tool selection guide") to buy this book.
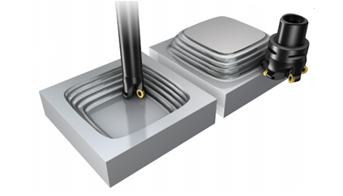
Typical copy milling
Profile milling cutter features
Copy milling cutters may all have round cutting edges or some milling cutters with round cutting edges, mainly with round insert milling cutters and ball end milling cutters. The profile cutter uses a circular blade. This change gives the profile cutter a number of advantages. Most of the benefits can be said to be the cutter for small back pockets and large feed round inserts. Ball-type milling cutters and inserts are shown below.
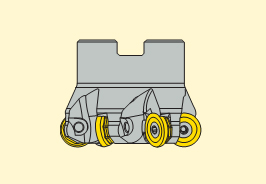
Milling cutter with round insert
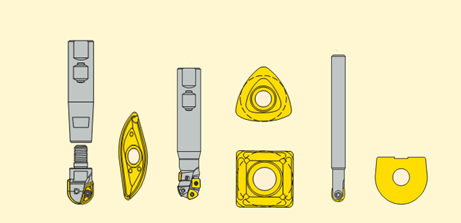
Ball head milling cutter and blade
The circular blade copy milling cutter has the following advantages:
(1) Cutting edge strength The circular blade has no sharp corners and can withstand greater tool deflection and vibration, allowing the rotation speed and the feed to be increased during machining, while reducing the risk of chipping.
(2) Large number of cutting edges With more available cutting edges, there are 4 to 8 effective indexings. This saves tool change time, increases processing efficiency, and increases economics.
(3) High cutting rate The circular insert can have a high metal cutting rate without requiring high machine power, and a higher feed rate than a right angle milling cutter due to the high blade strength.
(4) High precision of roughing The surface of the workpiece after rough machining with a circular blade is relatively flat, and semi-finishing can be easily performed. In some cases, even finishing can be directly performed.
Mold processing profiling milling cutter selection
Mold processing, especially the processing of its main cavity parts, relies mainly on various end mills. Usually, small molds are mostly processed by integral end mills. Large molds are considered to be economical and processing efficiency. Machine-clamp end mills with indexable inserts are often used for machining, but integral end mills are often used for finishing. The choice of the contour milling cutter body can be determined according to the application conditions (see Table 1).
Table 1 Tool selection for different working conditions
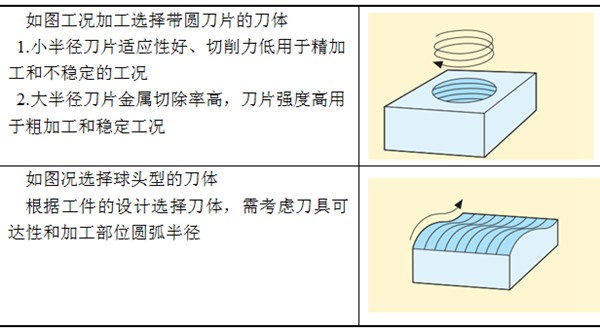
Mold processing can be divided into roughing, semi-finishing and finishing, and sometimes even super finishing. Roughing and semi-finishing processes generally use indexable tools, and the finishing process uses integral tools.
The main goal of die roughing is to pursue the maximum material removal rate per unit time and to prepare the geometric profile of the workpiece for semi-finishing. The roughing cavity is usually machined with a round insert tool, and the circular insert has a large arc radius and a large blade strength. The main goal of semi-finishing of the mold is to flatten the contour of the workpiece to ensure a uniform residual machining allowance on the surface of the workpiece after semi-finishing. The high-speed finishing process of the mold depends on the point of contact between the tool and the workpiece, and the contact point of the tool with the workpiece changes with the slope of the curved surface of the machined surface and the effective radius of the tool.
The commonly used knives in copy milling have four types of milling cutters, ball end milling cutters, interchangeable milling head ball end milling cutters and solid carbide ball end milling cutters. Table 2 compares these four commonly used copy milling cutters in consideration of machining stability and cost productivity.
Table 2 Selection of different types of milling cutters in profiling
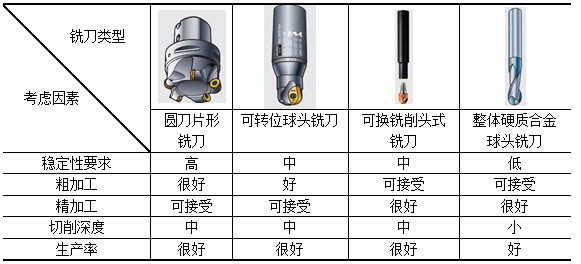
The indexable willow ball head milling cutter has small cutting force, high processing efficiency and easy to use, and is suitable for stamping die processing. The indexable disk milling cutter is most suitable for contour, cavity and contour processing, and is good at plastic molds. , die-casting, forging and stamping die; milling head can be combined with the shank, using many different shank types and lengths, many different cutter heads are high productivity; solid carbide ball-end milling cutters are generally used for small molds End mill processing, and the use of integral end mills in large mold finishing.
When the ball-end milling cutter is used to mill the free-form surface, the cutting speed of the end of the ball-end tool is zero. To ensure the machining accuracy, the cutting distance is generally the tip-tight distance. The tip of the ball-end milling cutter is stronger than the tip of the flat-end milling cutter. The distribution of the load on the blade is uniform. Therefore, the ball end mill has a longer service life under the same surface finishing conditions.
When using a ball end mill for surface finishing, the ball radius of the ball end mill should be selected as large as possible to increase tool rigidity and heat dissipation. Usually the radius of curvature of the finished surface should be greater than 1.5 times the radius of the tool to avoid sudden changes in the feed direction.
High alloy steel mold processing case example
1.54HRC high alloy steel material with high rough processing.
(1) Material: Hardened tool steel "ORVAR Supreme" 54HRC.
(2) Tool: CoroMill200.
(3) Machine tool: Matsura RAIII, 3-axis machine tool, maximum spindle speed 15000, power 7.5kW.
(4) Processing parameters: the number of teeth z is 4 rotation speed n is 954 rpm; the cutting speed vc is 150 m/min; the feed rate fz is 0.2 mm; the feed speed vf is 763 mm/min; the ratio of the back-feeding knife to the cutting width is ap /ae is 1/80% mm.
(5) Processing time: 37 minutes and 30 seconds.
High alloy steel mold Sandvik Coromant CoroMill 200
2. Car light mold processing
(1) Workpiece name: lamp mold.
(2) Workpiece material: 2738HH; material hardness: about 40HRC.
(3) Tool holder model: MST E50-SLSC8-180 (Jiehao MM medium hardness series milling tool), tool type: SR4×16×60×2F×D8.
(4) Processing parameters: n=6800r/min, vf=4000 r/min, ap=0.10mm, ae=0.15mm.
(5) Total processing time: 8h30min.
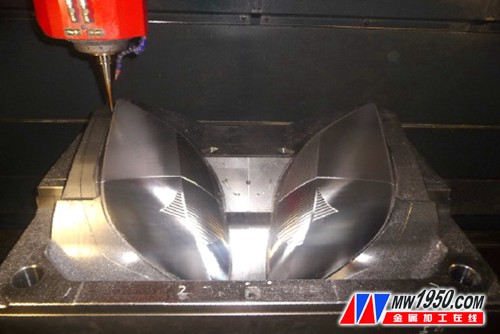
Car lamp mold processing diagram
Conclusion
In the mold manufacturing, there are large differences in the profile characteristics and materials of different parts, and the mold milling cutter used is also different. In terms of the profiling process in the mold processing, the profiling cutter mainly has a circular insert milling cutter and a ball end milling cutter. The selection of the profiling cutter requires the workpiece material, the occasion working condition, the cutting processing stability, and the cost. Several aspects of productivity processing accuracy are considered comprehensively. Only reasonable selection of tools can improve processing quality and processing efficiency, meet product aesthetics and functional requirements, and improve mold processing technology.
Wood Gasifier Generator,Wood Gasifier Power,Agriculutral Waste Gasification Power System,Wood Gasifier Power Systems
Henan Dianyan New EnergyTechnology Co. Ltd , https://www.cngasifier.com